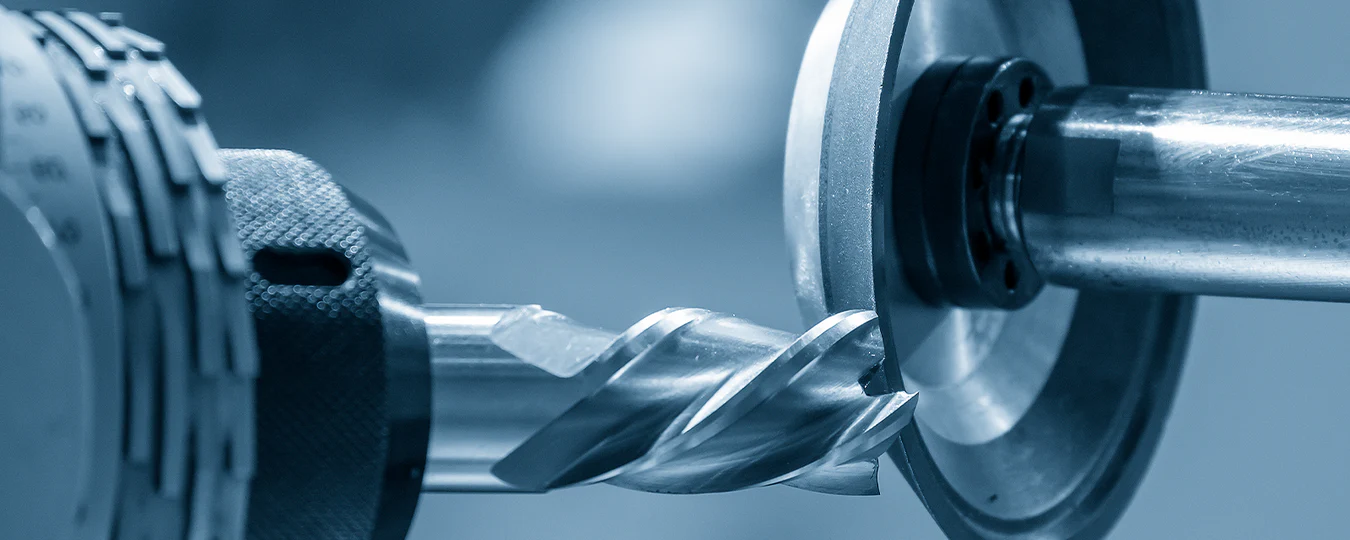
PRECISION GRINDING TECHNOLOGY
From prototyping to high volume production, BAUCOR® provides highest quality technical expertise and capabilities in manufacturing your cutting tools.
Diamond-coated parts have been coated with a layer of diamond particles. This coating is typically applied using electroplating or electroless plating, which involves depositing a layer of diamond particles onto the part's surface using an electric current or a chemical process. The diamond coating is applied in a thin layer, usually only a few micrometers thick, but it can significantly increase the wear resistance and durability of the part. The coating can also protect the part from corrosion and other forms of damage.
Diamond coatings are often used on parts subject to high wear levels, such as cutting tools, dies, and other mechanical components. The diamond coating can help extend these parts' lifespan by providing a wear-resistant surface resistant to abrasive wear and damage. Diamond coatings can also improve the performance of these parts by reducing friction and wear during use. It can help improve the efficiency of the machinery in which the coated parts are used, as well as reduce the downtime and repair costs associated with wear and damage.
From prototyping to high volume production, BAUCOR® provides highest quality technical expertise and capabilities in manufacturing your cutting tools.
BAUCOR® is highly specialized in manufacturing custom industrial blades. If you need your knives manufactured to your exact requirements, please contact us now.
Baucor designs, engineers, and manufactures highest quality precision diamond coated tools, wear parts and wear resistant parts to last longer than ever. Electroplating your wear parts, cutting tools with diamond will provide extra longer life, much better grinding capabilities. Whether you have a print or a rough sketch or even an idea that you need turned into a wear resistant component, Baucor is fully capable of manufacturing precision parts for machinery, aerospace, automative, oil-gas, renewable reenergy and for all other sectors using carbide parts to limit tool wear.
Understanding today's challenges in the design as well as product qualtity of wear resistance requirements, Baucor is here to undertake this challenge with you. Whether you are in converting, machinery, equipment, or any other industry, turn to Baucor just like thousands of others for the right and optimum solutions. At its highend facilities, Baucor is committed to designing and manufacturing precision wear resistant components.
From a size of a couple of millimeters to a size of 100", Baucor are highly specialized in manufacturing specialty tools including carbide components per sample, drawing or even an idea. If you need your specialty tools manufactured to your exact requirements, please contact us now get to a free quote. If you have a drawing, sketch or written specifications for the blade you need, please let us know or else we can design and engineer it for you.
Small or large, BAUCOR® manufactures all types and shapes of precision circular blades in nearly all materials available in the market.
Whether it is 5mm or 2500mm long, BAUCOR® has the right capacity and advanced capabilities to manufacture precision industrial blades.
Did you know that BAUCOR® has manufactured tens of thousands of precision punch blades? Get your quote today!
Manufacturing custom industrial blades is no easy task that anyone can handle. That's why BAUCOR® is here to help!
There are many advantages of using diamond-coated parts:
To coat a part with a diamond, we use electroplating. The manufacturing process includes:
BAUCOR® manufactures razor and straight blades as small as 5mm and as large as 2500mm.
Punch blades must be made to exact specs. Turn to BAUCOR® just like thousands of customers around the world.
Whether you need circular slitter blades or flat slitter blades, BAUCOR® is here to turn your design into precision part.
BAUCOR® manufactures precision top quality toothed blades in all shapes and form.
Need to make a slit or cut through your material as precise as possible? BAUCOR® pointed blades are of highest quality in the market.
Top and bottom shear and slitter blades from BAUCOR®.
American or European style! BAUCOR® has the correct holder for you!